
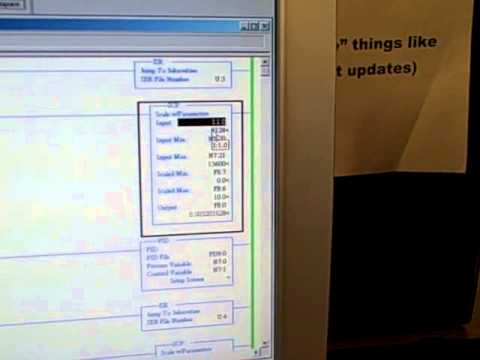
We recommend you use dependent gains for three reasons: it is more commonly used, it is the ISA Standard, and it is what was used in the Logix 500 platform. The only consequence of this choice is that the units of Reset and Rate (the I and D of PID) will have different meanings. There is no operational difference between the two: both methods work equally well in any situation. When setting up the PID block, you are given the option of using either dependent or independent gains. The first selection to be made is titled PID Equation. Open the PID blocks setup screen and select the Configuration tab. The most common strategy is to write to the setpoint using data that is coming in from a touchscreen, while a more complex strategy might allow adjustment of PID parameters from a touchscreen as well. The vast majority of PID applications will use both approaches to some degree. All of these data locations are listed in tables at the end of this document. The second approach is more sophisticated, where the various commands and data registers are written to from the ladder logic. You can perform PID on a process using as little as a tag for the PID instruction and a tag for the CV, then manually keying in a value for the setpoint, and finally entering parameters in the PID blocks setup screen. The simpler approach is to set control bits and write data directly in the block using RSLogix 5000. There are two approaches to manipulating the data within the PID block. In most cases leave PID Master Loop, Inhold Bit, and Inhold Value at zero unless you really plan to use them.Ģ. Leave Tieback at zero for now (it will be discussed in Step 13). Enter a tag for the Process Variable, keeping in mind the possibility of internal scaling (discussed in Step 11). Be sure to assign its tag the Data Type PID. Insert the PID block from the Special menu. If, for example, you have an industrial oven which is heated by a gas burner, can you disconnect the mechanical linkage between the servo motor and the throttle and then adequately control the temperature by physically moving the throttle? If you cant, then maybe you have a problem that the most finely tuned PID loop can never control! Assuming that you can control your process manually, continue on 1.

Step number one in the solution of any control problem is to first assure that the process can be controlled well. If you are not already familiar with PID control, we strongly recommend you read one of our Getting Started Guides to PID Control, and if you are not familiar with PLC programming, we strongly recommend you read our Getting Started Guide to Programmable Logic Controllers. Note carefully that the methods used here are not universally applicable nor are they the only means of arriving at a PID solution to your control application. It is assumed that the reader has three important skills: a good working knowledge of PID, a good working knowledge of the Logix 5000 platform, and a good working knowledge of the process and system to which the PID block is to be applied. Quick Start Guide to Using the PID Block in Logix 5000Ģ009 SimpleSolvers, LLC Copyrighted material! Do not copy or otherwise distribute without express written permission of SimpleSolvers, LLC
